The potentially transformative capabilities of advanced AI, automation, and robotics technology are ushering in a new era for manufacturing. Yet, at the same time, extracting value from the digital transformation is more complicated than it might seem. Case in point—an overwhelming 88% of companies report difficulties measuring value from technological investments.
The same report found that 85% of companies struggle to simultaneously update operating models to accommodate their new visions and cover the upfront investment costs for new technology. These challenges are further compounded for 84% of companies by the need to train workforces on operating new technology upgrades.
This gap between the potential of new manufacturing technology and the challenges surrounding its integration can pose a problem for industry leaders. Both the value and potential losses of investing now are somewhat shrouded in mystery.
However, the solution to this confusion is a greater understanding of the challenges and opportunities that new manufacturing tools will likely present in the coming year.
Developing Trends in New Manufacturing Technology for 2024
To better grasp what 2024 will bring to the manufacturing industry, one must understand the trendy technology that may shape the year.
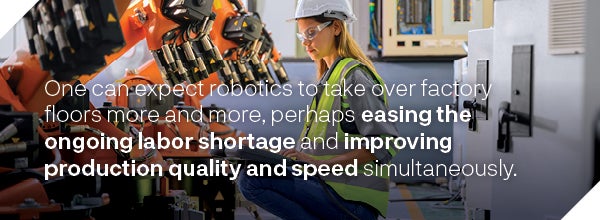
AI and automation will likely create seismic shifts thanks to operational procedures like predictive maintenance, design optimization, and supply chain management. One can expect robotics to take over factory floors more and more, perhaps easing the ongoing labor shortage and improving production quality and speed simultaneously.
In certain manufacturing processes, technology like 3D printers may become staple components of new workflows. In others, virtual solutions like extended reality can aid design and production.
All the while, concepts like sustainability, reshoring, and servitization are emerging as key trends.
One of the most complex new manufacturing concepts is Industry 4.0. This is a comprehensive overhaul of manual workflows in favor of smart technologies capable of automation. Systems like connected Internet of Things (IoT) devices and cloud computing tech stacks will likely transform traditionally manual processes moving forward.
The summation of all these changes suggests that 2024 stands to push manufacturing forward into the age of automation and robotics. However, such a comprehensive transformation isn’t necessarily easy to conduct—and the manufacturing industry isn’t immune to the growing pains that come with new technologies, making it critical to research trends ahead of time.
Challenges and Opportunities for Manufacturing Decision-Makers
The culmination of new technology advancements, turbulent economic conditions, disruptions to supply chains, and labor shortages are bound to make 2024 a fickle year.
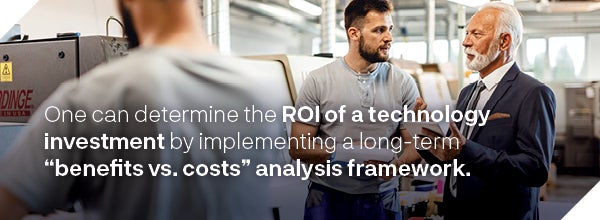
Navigating the complexities that are likely to characterize manufacturing in the near future isn’t a small task. Most leaders may need extensive research and planning to find the best path forward. With this in mind, let’s explore some of the most prominent challenges and opportunities that could characterize manufacturing markets in 2024.
Assessing Tech ROI Remains Difficult
Recent surveys indicate nearly half of executives—48% to be exact—agree that they’re behind their competitors in adopting new technologies. Of course, this trend varies across department leaders. For instance, while 68% of COOs say their company is behind in new technology adoption, only 33% of tax leaders agree.
The differential across departments might be the need to innovate and push efficiency metrics in workflows. Certain internal workflows reward bold decision-making and risk-taking more than others, and the data bears this idea out.
The factory floor is where slight operational improvements might yield exponential returns. However, measuring the dollar-to-dollar impact of technology on every aspect of productivity can challenge many business leaders’ perceptions of the value of new manufacturing technology investments.
One can determine the ROI of a technology investment by implementing a long-term “benefits vs. costs” analysis framework.
Conducting pilot projects and research-based risk mitigation before buying into new technology can help leaders get an idea of the returns prior to making any decisions. At the same time, banking experts can help leaders with detailed numerical calculations regarding the ultimate returns an investment might yield.
The Challenge of the Labor Shortage
The ongoing labor shortage has presented a preeminent concern for some manufacturing executives in 2023. Attracting and retaining skilled talent may take longer and cost more in a tight labor market; competitor initiatives to attract their own talent can also cause increased turnover and wage hikes that slim down company margins.
Turnover is a notable concern for many manufacturers in the current labor market. This doesn’t just impede daily operations during the rehiring and training process but can also drag down worker morale.
However, the outlook seems to be easing at the moment. According to the PWC, 74% of executives recently indicated they are attracting and retaining the talent they need. This shift is much needed for manufacturers—but the question is, what’s driving it?
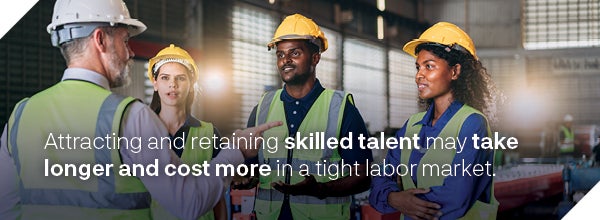
It’s difficult to pinpoint one factor. However, heightened internal resource allocation to hiring and training certainly presents a key solution. Workforce development morphed into a key priority for many over the past year, and it’s likely to carry on into 2024.
However, this isn’t the only factor. Advancements in robotics and automation are making it possible for some manufacturers to operate with heightened efficiency by curtailing manual stopgaps in production.
Inflation and Fears of Recession
Inflation presented one of the most prominent challenges across all sectors in 2023—but manufacturing was hit particularly hard by rising prices over the year. Meanwhile, supply chain shortages and disruptions may compound ballooning costs to further slash profits by sending transportation, raw materials, and energy expenses soaring.
Much of 2023 was spent in suspense, waiting for a recession that never entirely manifested. However, the volatility of the economy has left many manufacturers wondering if said recession was simply deferred to 2024 rather than dodged entirely.
Subsequently, this may lead many executives to question the wisdom of making new manufacturing technology investments prior to a potential downturn. However, other decision-makers are latching onto the vast efficiency gains and production cost cuts that advanced new technologies like robotics, AI, and automation can bring as a barrier against spiraling inflation .
For example, an automated factory floor can operate at breakneck speed around the clock. Furthermore, the exorbitant overtime costs it might otherwise take to ramp up production to this scale are usually not a factor for companies that invest in automation. Waste-reducing measures like closed-loop production cycles can further help combat inflation by reducing the need for raw materials.
Supply Chain Disruption
While rising expenses are often a serious consequence of broken supply chains, the impacts of global shipping disruptions extend beyond straightforward costs. Production schedules can experience severe delays as a result of blocked ports and limited resource extraction; a lack of necessary components can also impact product quality.
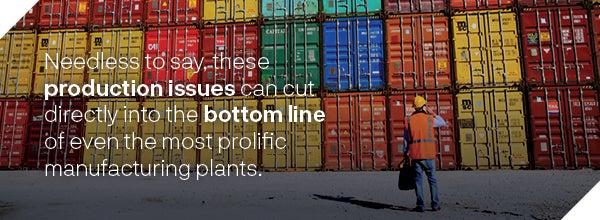
Needless to say, these production issues can cut directly into the bottom line of even the most prolific manufacturing plants. There are several strategic moves one can make to try to work around frequent delayed shipments, first and foremost being a diversification of suppliers. This way, a manufacturer isn’t entirely reliant on a single source for parts and handling. A slight break in the supply chain will (ideally) be but a minor inconvenience instead of a total disaster.
At the same time, tools like AI and machine learning can optimize inventory management through predictive models, thereby avoiding both overstock and stockouts. Also, collaboration with competitors can help manufacturers shore up operations against market disruptions.
AI and Automation
The integration of automation and AI into daily operational processes may be shaping up to be one of the most prominent trends in 2024. In fact, 46% of executives intend to invest in generative AI in the next 12 to 18 months—and out of these respondents, 67% say they plan to use this AI investment to support their business model. Similarly, 61% are closely watching and engaging with the development of policy regarding the technology.
There are many potential practical uses of AI and automation in manufacturing and several key operational areas that provide immediate improvement stand out in particular.
For example, predictive maintenance can analyze data from machinery sensors to estimate mechanical failures before they occur. This allows maintenance to occur before these failures, eliminating costly production delays, improving output quality, and extending equipment lifespans.
Furthermore, AI can help optimize quality control processes;. AI-driven visual inspection systems detect defects and inconsistencies in products faster and more accurately than human inspectors.
Finally, real-time analytics allow manufacturers to optimize processes in the midst of production to increase overall performance.
Sustainability
In competitive sectors, setting oneself apart is essential. However, differentiation can be challenging to pull off—unless a manufacturer can resolve notable issues before their competitors.
Many consumers and manufacturers are developing greater awareness regarding the sustainable production of goods and services. Companies find themselves under growing pressure to reduce wasteful practices and incorporate recycled materials. However, the impetus to adopt sustainable manufacturing practices runs beyond mere public perception. Unpredictable weather and geopolitical events dominate news headlines around the globe—and add to supply chain problems already plaguing the industry.
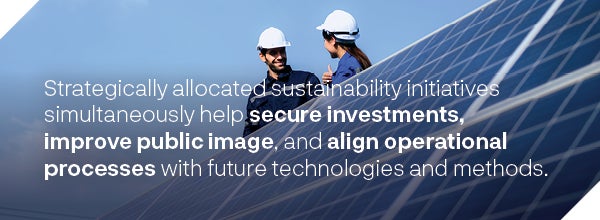
However, this growing crisis among consumers and manufacturers presents a unique opportunity for differentiation in the manufacturing sector. These issues are gaining prominence for investors, with 69% reporting that they would increase contributions to companies that successfully address sustainability issues directly affecting the company’s processes and performance.
At the same time, 69% of leaders agree that they’re ready to comply with upcoming sustainability reporting requirements—yet only 23% of them reported that they were actively planning disruption contingencies. Clearly, there’s a gap in preparedness when it comes to sustainability. Therefore, strategically allocated sustainability initiatives simultaneously help secure investments, improve public image, and align operational processes with future technologies and methods.
Considering this, focusing on sustainability in 2024 presents an excellent opportunity for manufacturers. To do so, companies can focus on the Corporate Sustainability Reporting Directive (CSRD), which aims to ensure environmental impact and sustainability practices through transparency. Furthermore, shifting to renewable energy sources and more power-efficient daily usage can make a huge difference.
How to Financially Prepare for Bold Investments in Manufacturing Technology
When it comes to new manufacturing technology, the final piece of the puzzle for many business leaders is determining the financial viability of the investment.
Most companies seek to maintain sufficient liquidity to weather an economic storm. However, this can sometimes create tension with the competitive need to innovate and advance. Resolving the strain between these two factors requires extensive financial research and preparation.
To this end, reviewing cash flow projections can prove a helpful building block. Doing so can help you anticipate future income and expenses, aiding in making informed investment decisions.
Of course, to truly get a firm hold on the value of an investment, many companies will need to work with an external banking partner. Said partnership can help one better understand key goals and help craft customizable financial strategies to attain them.
Sourcing New Manufacturing Technology With a Reliable Banking Partner
New manufacturing technology is pushing the industry forward faster than ever. Advancements in AI, automation, and robotics are helping companies make major strides in terms of efficiency and cost reduction; however, this progress is somewhat tempered by uncontrollable factors like inflation, supply chain disruption, and even the growing business consequences of environmental sustainability.
That being said, technology can potentially mitigate many of the impacts of these notable challenges, thereby further adding to the potential returns they can generate for investors.
Regardless of a manufacturer’s specific growth goals for 2024, the proper allocation of funds is critical to meeting them. Reach out to the financial partners at Bank of Blue Valley, a division of HTLF Bank to get started planning, today!
These links are being provided as a convenience and for informational purposes only; they do not constitute an endorsement or an approval by HTLF of any of the products, services, or opinions of the corporation or organization or individual. HTLF bears no responsibility for the accuracy, legality or content of the external site or for that of the subsequent links. Contact the external site with questions regarding its content and privacy policy.